简单分析轴承箱加工新思路
2018-03-02 17:30:54· 来源:机工机床世界 作者:陆雪梅
轴承箱是风机传动组的主要组成部分,一般采用铸铁件,铸件质量须符合JB/T 6887—1993风机用铸铁件技术条件。其形状复杂,工艺难度大,精度要求高。尤其是轴承孔的尺寸精度和同轴度,对于风机运行的可靠性至关重要,应作为质量管理点予以监控。
轴承箱是风机传动组的主要组成部分,一般采用铸铁件,铸件质量须符合JB/T 6887—1993风机用铸铁件技术条件。其形状复杂,工艺难度大,精度要求高。尤其是轴承孔的尺寸精度和同轴度,对于风机运行的可靠性至关重要,应作为质量管理点予以监控。
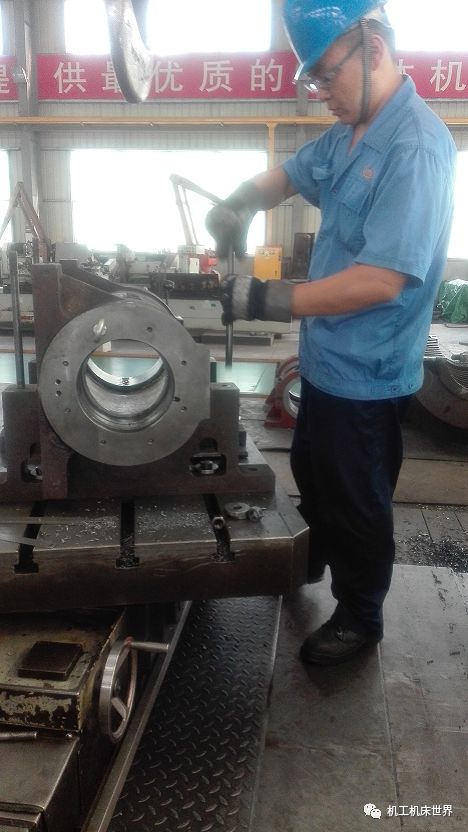
一、通风机机械运转试验内容和要求
1、机械运转试验应按GB 13275—91规定执行,风机应在无载荷情况下起动。连续运转时间在轴承温升稳定后不得少于20min,在轴承表面测到的轴承温度一般不得高于环境温度40℃。
2、轴承部位的振动速度有效值不得超过6.3mm/s,符合JB/TQ 334—87通风机振动精度规定。
二、通风机运转中的主要故障
通风机运转中的主要故障有:①轴承箱剧烈振动。②轴承温升过高。③电动机电流过大和温升过高。
三、轴承箱加工工艺要求
轴承箱加工质量的好坏对风机运行的可靠性至关重要。针对通风机,我公司机械运转试验标准规定,轴承部位的振动速度有效值不得超过4mm/s。
而针对低温升蒸汽压缩机这一高端装备,我公司机械运转试验标准规定,轴承部位的振动速度有效值不得超过2.3mm/s,从技术上对轴承箱加工提出了严格的高要求。
轴承箱的结构型式因机号大小和用途而异,有整体与剖分结构,水冷与风冷以及轴承座(Y5-47型)型式之分。
针对整体式轴承箱,一般工艺流程为:铸件退火→划线、铣(刨)→钻孔→粗镗→精镗→划线、钻孔→检验。
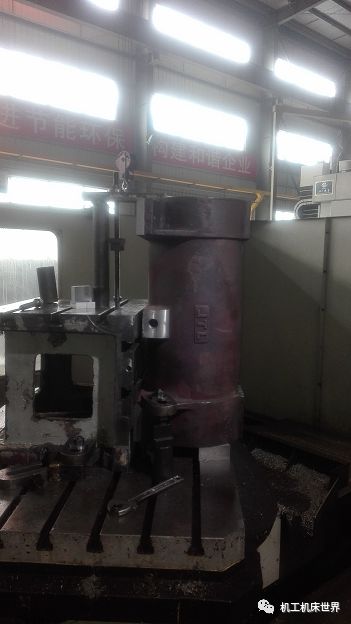
四、影响尺寸及位置精度的主要因素及改善措施
1、测量误差
由于量具制造误差、测量方法误差等引起。
改善措施:根据精度要求,合理选用测量方法及量具量仪;正确使用量具,控制环境温度。
2、机床误差
包括机床几何误差、机床热变形与受力变形造成的误差。
改善措施:提高机床几何精度;减小或补偿机床热变形及受力变形。
3、刀具误差
包括刀具几何形状制造误差与刀具安装误差;刀尖尺寸磨损等。
改善措施:提高成形刀具刀刃的制造精度;提高刀具安装精度;改进刀具材料;选用合理切削用量;以及自动补偿刀具磨损。
4、工件定位基准面误差,找正误差
改善措施:提高定位基准面、找正基准面的精度。
5、工件定位基准和设计基准不重合
改善措施:提高设计基准与定位基准之间的位置精度。
6、工件残余应力
加工时破坏了残余应力的平衡;工件残余应力处于不稳定的平衡状态。
改善措施:粗、精加工分开;进行时效处理。
7、工艺系统热变形
包括机床热变形、工件热变形和刀具热变形,以及工件加工刚结束时所测量的尺寸不能反映工件的实际尺寸。
改善措施:寻找热源,减少发热,移出、隔离、冷却热源;机床热平衡后再加工;进行充分有效的冷却;减小刀杆悬伸长度,增大刀杆截面;粗、精加工分开;根据工件热变形规律,测量时适当补偿,或在冷态(室温)下测量。
8、工艺系统受力变形
毛坯余量不均或材料硬度不均引起切削力变化,使毛坯的形状误差部分地复映到工件上;以及传动力、惯性力、重力和夹紧力的影响。
改善措施:改进刀具几何角度以减小切削抗力;安排预加工工序;合理选择夹紧方法和夹紧力大小。
五、工艺改进试制方案
附图所示为低温升蒸汽压缩机轴承箱零件结构,工件材质为QT500-7,两轴承室尺寸不同,其对轴承箱的加工同轴度要求为0.03mm之内,表面粗糙度值Ra=0.8μm。针对此工件的技术要求,全面考虑影响轴承箱尺寸精度及位置精度的主要因素,对原先的轴承箱机加工工艺流程进行了改进。
确定新的工艺试制方案为:铸件退火→二次退火→划线,粗、精铣(留磨削余量或数控铣削余量)→粗镗→退火→磨(或数控铣)→数控半精镗→放置一夜(自由状态)→三坐标测量仪检测→数控精镗→三坐标测量仪检测→数控镗钻孔→划线、镗钻孔→划线、钻孔→检验。
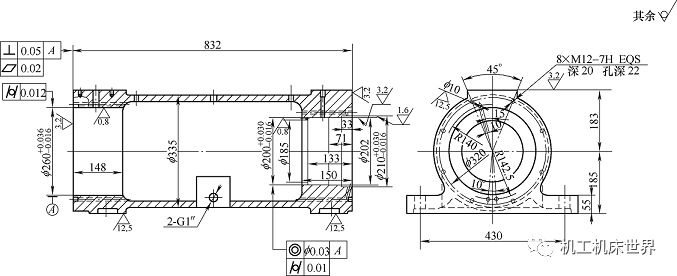
六、试制及验证
1、外协需退火处理的铸件,回公司后进行二次退火
进一步消除铸件内应力,细化均匀组织,降低硬度,改善切削加工性能。
2、粗、精铣轴承箱底脚面和上平面,留磨削余量或数控铣加工余量0.3~0.5mm
3、粗镗,留半精镗、精镗余量3mm;而后进行三次退火
进一步消除铸件内应力。
4、磨加工(或数控铣)轴承箱上平面、底脚面,表面粗糙度值Ra=0.8μm,提高定位基准面精度。
5、数控半精镗
两轴承室工艺要求加工尺寸分别为φ259+0.036 -0.016mm、φ199+0.030 -0.016mm,表面粗糙度值Ra=0.8μm;左端面表面粗糙度值Ra=1.6μm;其余各部位均留精镗加工余量1mm。工艺要求规定半精镗最后一刀时,留光刀余量0.2mm。半精镗加工后,将工件放置一夜(压紧用螺栓需全部松开),第二天采用三坐标测量仪进行尺寸精度及位置精度检测。
采用数控半精镗加工,以提高机床几何精度。采取调头镗加工,以减小刀杆悬伸长度、增大刀杆截面;采用数控进口刀具;选用合理切削用量;进行充分有效的冷却;对两轴承室及左端面进行尺寸精度及位置精度控制及验证,可为精镗加工提供经验,同时可以提高找正基准面精度。
6、校正、数控精镗
精镗加工时操作方法及注意点同(5)数控半精镗。数控精镗后采用三坐标测量仪进行尺寸精度及位置精度检测。
通过工艺改进试制和三坐标测量仪验证,成功加工出符合技术要求的轴承箱。
七、确定工艺方案
在工艺改进试制方案运行成功的基础上,我们确定出轴承箱的加工工艺方案。该工艺方案对数控半精镗加工作出新的工艺要求,各部位均留精镗加工余量1mm。而后将工件放置一夜(压紧用螺栓需全部松开),第二天进行数控校正、精镗。精镗操作方法及注意点同工艺试制时的数控精镗。采用三坐标测量仪进行尺寸精度及位置精度检测。
最终确定工艺方案为:铸件退火→二次退火→划线,粗、精铣(留磨削余量或数控铣削余量)→粗镗→退火→磨(或数控铣)→数控半精镗(各部位留余量1mm)→放置一夜(自由状态)→第二天数控校正、精镗→三坐标测量仪检测→数控镗钻孔→划线、镗钻孔→划线、钻孔→检验。
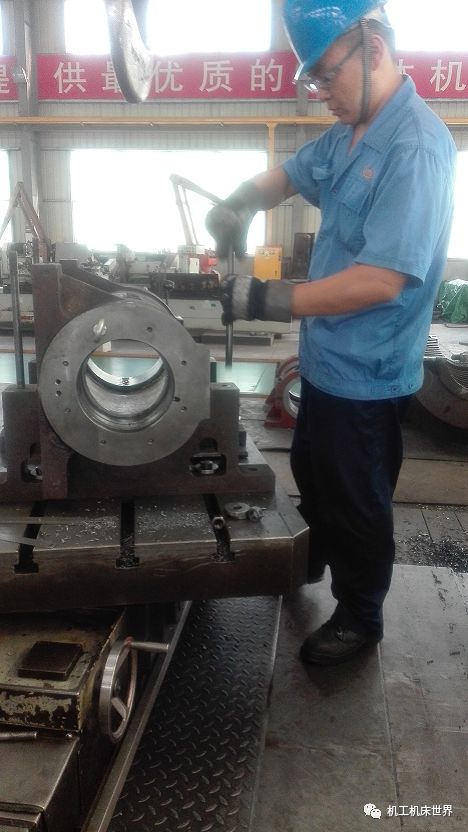
一、通风机机械运转试验内容和要求
1、机械运转试验应按GB 13275—91规定执行,风机应在无载荷情况下起动。连续运转时间在轴承温升稳定后不得少于20min,在轴承表面测到的轴承温度一般不得高于环境温度40℃。
2、轴承部位的振动速度有效值不得超过6.3mm/s,符合JB/TQ 334—87通风机振动精度规定。
二、通风机运转中的主要故障
通风机运转中的主要故障有:①轴承箱剧烈振动。②轴承温升过高。③电动机电流过大和温升过高。
三、轴承箱加工工艺要求
轴承箱加工质量的好坏对风机运行的可靠性至关重要。针对通风机,我公司机械运转试验标准规定,轴承部位的振动速度有效值不得超过4mm/s。
而针对低温升蒸汽压缩机这一高端装备,我公司机械运转试验标准规定,轴承部位的振动速度有效值不得超过2.3mm/s,从技术上对轴承箱加工提出了严格的高要求。
轴承箱的结构型式因机号大小和用途而异,有整体与剖分结构,水冷与风冷以及轴承座(Y5-47型)型式之分。
针对整体式轴承箱,一般工艺流程为:铸件退火→划线、铣(刨)→钻孔→粗镗→精镗→划线、钻孔→检验。
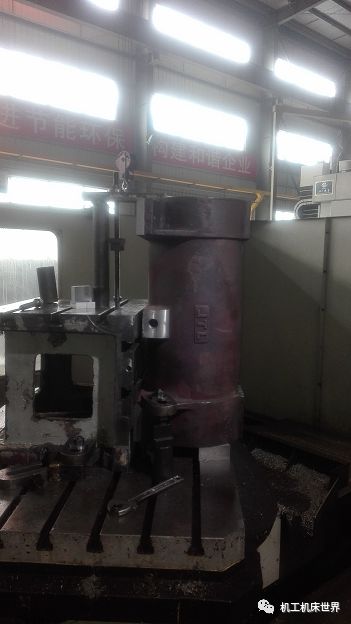
四、影响尺寸及位置精度的主要因素及改善措施
1、测量误差
由于量具制造误差、测量方法误差等引起。
改善措施:根据精度要求,合理选用测量方法及量具量仪;正确使用量具,控制环境温度。
2、机床误差
包括机床几何误差、机床热变形与受力变形造成的误差。
改善措施:提高机床几何精度;减小或补偿机床热变形及受力变形。
3、刀具误差
包括刀具几何形状制造误差与刀具安装误差;刀尖尺寸磨损等。
改善措施:提高成形刀具刀刃的制造精度;提高刀具安装精度;改进刀具材料;选用合理切削用量;以及自动补偿刀具磨损。
4、工件定位基准面误差,找正误差
改善措施:提高定位基准面、找正基准面的精度。
5、工件定位基准和设计基准不重合
改善措施:提高设计基准与定位基准之间的位置精度。
6、工件残余应力
加工时破坏了残余应力的平衡;工件残余应力处于不稳定的平衡状态。
改善措施:粗、精加工分开;进行时效处理。
7、工艺系统热变形
包括机床热变形、工件热变形和刀具热变形,以及工件加工刚结束时所测量的尺寸不能反映工件的实际尺寸。
改善措施:寻找热源,减少发热,移出、隔离、冷却热源;机床热平衡后再加工;进行充分有效的冷却;减小刀杆悬伸长度,增大刀杆截面;粗、精加工分开;根据工件热变形规律,测量时适当补偿,或在冷态(室温)下测量。
8、工艺系统受力变形
毛坯余量不均或材料硬度不均引起切削力变化,使毛坯的形状误差部分地复映到工件上;以及传动力、惯性力、重力和夹紧力的影响。
改善措施:改进刀具几何角度以减小切削抗力;安排预加工工序;合理选择夹紧方法和夹紧力大小。
五、工艺改进试制方案
附图所示为低温升蒸汽压缩机轴承箱零件结构,工件材质为QT500-7,两轴承室尺寸不同,其对轴承箱的加工同轴度要求为0.03mm之内,表面粗糙度值Ra=0.8μm。针对此工件的技术要求,全面考虑影响轴承箱尺寸精度及位置精度的主要因素,对原先的轴承箱机加工工艺流程进行了改进。
确定新的工艺试制方案为:铸件退火→二次退火→划线,粗、精铣(留磨削余量或数控铣削余量)→粗镗→退火→磨(或数控铣)→数控半精镗→放置一夜(自由状态)→三坐标测量仪检测→数控精镗→三坐标测量仪检测→数控镗钻孔→划线、镗钻孔→划线、钻孔→检验。
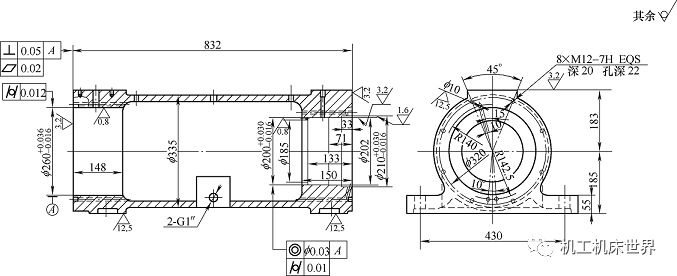
六、试制及验证
1、外协需退火处理的铸件,回公司后进行二次退火
进一步消除铸件内应力,细化均匀组织,降低硬度,改善切削加工性能。
2、粗、精铣轴承箱底脚面和上平面,留磨削余量或数控铣加工余量0.3~0.5mm
3、粗镗,留半精镗、精镗余量3mm;而后进行三次退火
进一步消除铸件内应力。
4、磨加工(或数控铣)轴承箱上平面、底脚面,表面粗糙度值Ra=0.8μm,提高定位基准面精度。
5、数控半精镗
两轴承室工艺要求加工尺寸分别为φ259+0.036 -0.016mm、φ199+0.030 -0.016mm,表面粗糙度值Ra=0.8μm;左端面表面粗糙度值Ra=1.6μm;其余各部位均留精镗加工余量1mm。工艺要求规定半精镗最后一刀时,留光刀余量0.2mm。半精镗加工后,将工件放置一夜(压紧用螺栓需全部松开),第二天采用三坐标测量仪进行尺寸精度及位置精度检测。
采用数控半精镗加工,以提高机床几何精度。采取调头镗加工,以减小刀杆悬伸长度、增大刀杆截面;采用数控进口刀具;选用合理切削用量;进行充分有效的冷却;对两轴承室及左端面进行尺寸精度及位置精度控制及验证,可为精镗加工提供经验,同时可以提高找正基准面精度。
6、校正、数控精镗
精镗加工时操作方法及注意点同(5)数控半精镗。数控精镗后采用三坐标测量仪进行尺寸精度及位置精度检测。
通过工艺改进试制和三坐标测量仪验证,成功加工出符合技术要求的轴承箱。
七、确定工艺方案
在工艺改进试制方案运行成功的基础上,我们确定出轴承箱的加工工艺方案。该工艺方案对数控半精镗加工作出新的工艺要求,各部位均留精镗加工余量1mm。而后将工件放置一夜(压紧用螺栓需全部松开),第二天进行数控校正、精镗。精镗操作方法及注意点同工艺试制时的数控精镗。采用三坐标测量仪进行尺寸精度及位置精度检测。
最终确定工艺方案为:铸件退火→二次退火→划线,粗、精铣(留磨削余量或数控铣削余量)→粗镗→退火→磨(或数控铣)→数控半精镗(各部位留余量1mm)→放置一夜(自由状态)→第二天数控校正、精镗→三坐标测量仪检测→数控镗钻孔→划线、镗钻孔→划线、钻孔→检验。
编辑推荐
最新资讯
-
辐射亚太,链接全球——采埃孚再制造
2025-07-30 11:46
-
思看科技发布子品牌SCANOLOGY,全球
2025-07-30 11:06
-
风雨不动安如山——比亚迪叉车构筑“
2025-07-30 08:48
-
NEAS CHINA 新能源汽车技术与生态链
2025-07-29 09:52
-
三维扫描革新碾磨机辊套检测,效率与
2025-07-25 10:46