机器人扫描仪执行自动化装配检查测试
总部位于美国华盛顿州的Dynacraft估算是PACCAR中型和重型卡车零部件的多元化全球制造商。40多年来,Dynacraft一直为该公司的卡车制造部门和PACCAR零部件部门提供高质量的组件,子组件和专业服务。
据汽车制造网获悉,总部位于美国华盛顿州的Dynacraft估算是PACCAR中型和重型卡车零部件的多元化全球制造商。40多年来,Dynacraft一直为该公司的卡车制造部门和PACCAR零部件部门提供高质量的组件,子组件和专业服务。
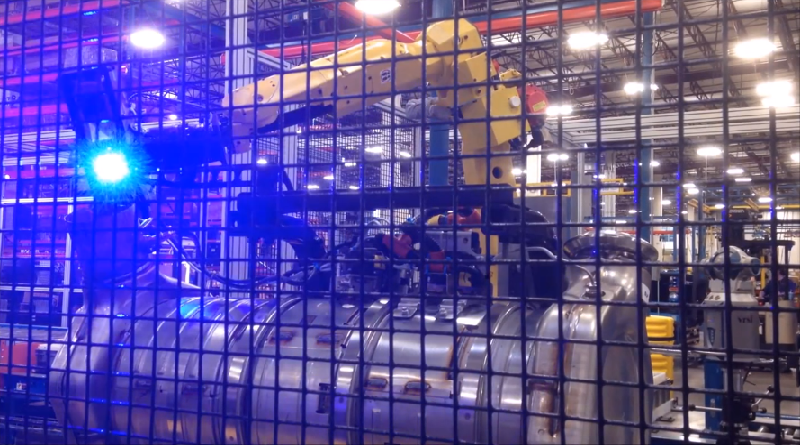
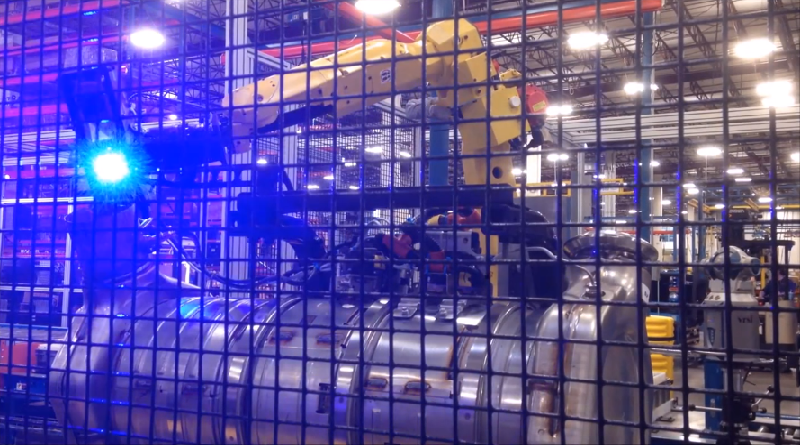
挑战
Dynacraft生产质量工程师Mario Caudillo解释说:“我们目前正在生产的2017新型排放系统的其中一项要求是我们的供应商质量小组要求对排放组件进行100%的检查。到目前为止,我们正在执行一项标准抽样计划,因此从样本计划到百分之百的检验都是一个相当大的挑战。”
尽管Dynacraft每天通过其生产线运行超过200个装配,但一个手动测量臂和一些技术人员足以跟上样品测试。然而,Dynacraft质量团队确定他们绝对没有办法用他们现有的流程进行100%的检查。因此,他们需要一个自动化的解决方案来满足客户的期望。
在与Dynacraft合作之前,Caudillo曾在一家主要的原始设备制造商(OEM)工作过,他有一些可以帮助解决困境的设备的经验。需要找到合适的公司,让合适的人能够推动项目的进程。
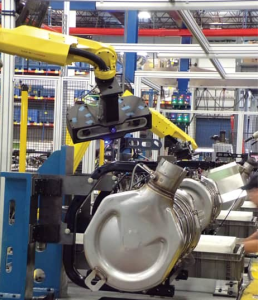
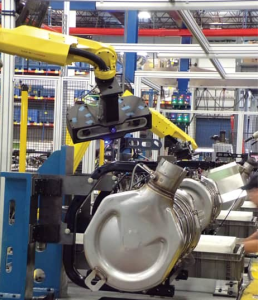
“我已经和一些公司谈论过这个项目,由于他们最终的技术限制,他们无法提供我们所要求的,” Caudillo说。“当我接触Variation Reduction Solutions,Inc.(VRSI)并开始与Evan Asher和Mike Kleemann交谈时,他们提出了正确的解决方案,能够启动这个项目并将其从底层移至应用程序。”
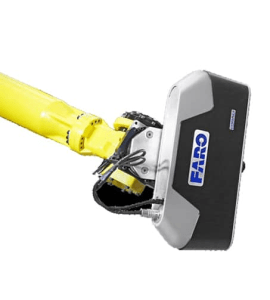
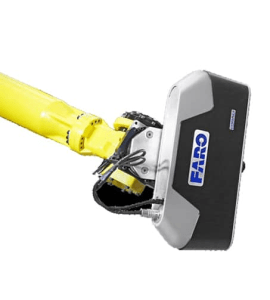
VRSI
VRSI拥有一批经验丰富的专家团队,自1998年以来,VRSI一直致力于为客户提供最先进的视觉,计量,工业机器人指导和自动化检测集成解决方案。
VRSI项目工程师Evan Asher说:“我们团队所做的大部分工作至少是半定制的。每个项目都是专门针对客户的应用和需求进行修改的。我们有一些与其他项目类似的项目,但不可避免地每个客户都有稍微不同的流程,但需求略有不同。根据问题是什么,我们为此定制解决方案。”
Dynacraft的理想解决方案必须符合尺寸规格,使其能够适应车间的在线工作单元,完全自动化,并且能够测量具有50到60个变化的6英尺长罐,并需要在65秒内完成。
“当一个项目需要将计量与工厂自动化相结合时,通常会有一个重要的系统工程组件,” VRSI总工程师兼航空航天组经理Mike Kleemann解释说。“我们从需求开始,然后向后工作,以确定需要结合使用以获得最佳解决方案的测量,自动化,控制和集成元素的组合。”
VRSI采用的一个系统组件是FANUC机器人手臂以及FARO Technologies钴阵列成像仪。
Asher说:“我们与FARO合作的部分原因是因为他们是一个非常可靠的供应商。有了Cobalt,我们发现准确性和视野都适合这个应用。它可以即插即用,将其插入计算机,可以立即开始滚动,因此证明它相对无缝的。”
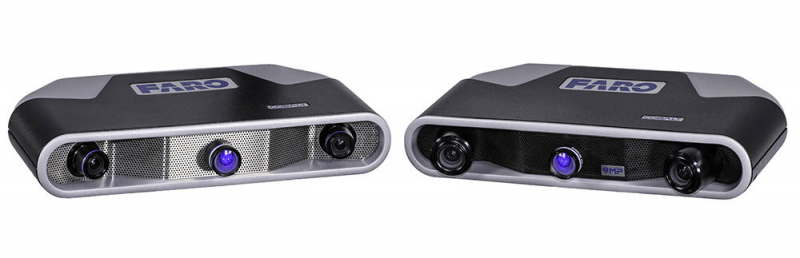
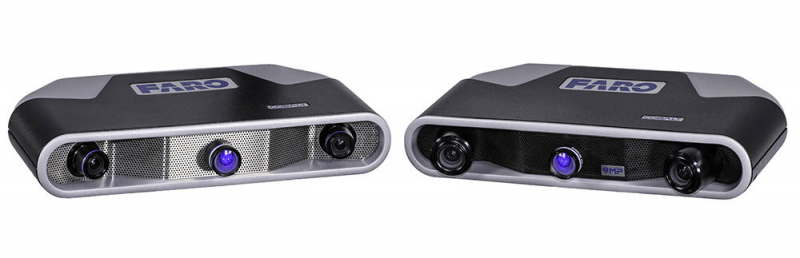
选择扫描仪时,同一组件上的表面光洁度变化也是一个考虑因素。
“发射组件的表面有多个金属表面,” Asher解释说。“ 有些是光亮的,有些是无光泽的,有些是中间的,更像是黑色的无光泽金属。此外,Cobalt必须测量表面的角度(由于空间限制)会导致差异。所以,我们所做的是,我们为每个位置调用了不同的曝光设置。有时一个曝光设置是足够的,有时我们需要多个曝光设置。为了有效捕捉某些特征,我们实际拍摄了三种不同的曝光,以实现正确的测量。”
钴的高动态范围及其测量光泽表面的能力使其成为在线工厂测量解决方案的自然选择。
适应制造流程
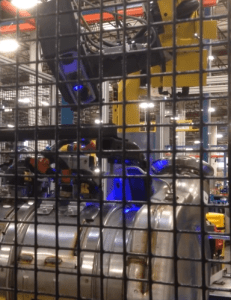
“我们的首要任务是根据印刷品的几何尺寸和公差方案(GD&T)获得基准方案,” Caudillo解释道。“由于它们放置在组件中的位置,因此组装中的基准点的位置很难获得。这是VRSI能够在Cobalt系统和机器人上做得很好的东西。”
在设计百分之百的检测系统时,管理生产空间需求是一个不小的挑战。
Asher说:“我们必须测量的四个特征中有两个是非常狭窄的区域。为了测量所有的特征,Cobalt必须处于非常特定的角度。在传感器的视野与机器人的关节之间,我们能够找到合适的位置来获得这些特征。”
最大限度地提高混合生产线的系统灵活性
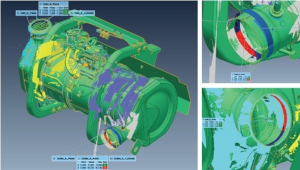
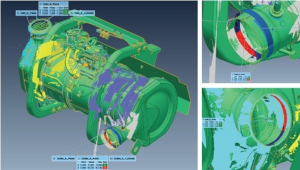
这个项目最难的部分之一是试图确定捕获这些组件进口和出口位置的所有不同变化的最佳方法。这些变化都具有独特的入口和出口位置,就入口和出口端口的位置的x和y配置而言。
“Cobalt传感器真的给了我们很大的灵活性,” Asher说。“ 由于Cobalt传感器视场的体积,我们所测量的所有部件尽管位置稍有不同,但都适合该视场的体积。尽管我们正在处理不同的部件,但从Cobalt的角度来看,我们只能使用一个机器人Cobalt位置来测量该位置上的20多种不同配置,而不是拥有20个不同的机器人位置。”
换句话说,该系统可以用六个机器人位置而不是数百个获得50到60个变化的数据。这种功能节省了时间,精力以及他们必须编写的例程数量,以及需要运行多少例程才能捕获所有必需的数据。
在每个机器人位置,Cobalt收集数据并创建点云。相关的点云必须“拼接”在一起,形成每个排放组件的完整数据集。为了准确地将这些点云缝合在一起,Cobalt位置在初始设置过程中进行了记录。这是通过使用FARO Vantage激光跟踪仪完成的。
“机器人校准通常意味着您可以使用激光跟踪器数据通过更新其运动学模型来提高机器人的体积精度,” Kleemann解释说。“我们在这里没有这样做,因为有少量离散职位。Vantage激光跟踪仪用于初始记录机器人位置。然后,检查系统依靠机器人的可重复性来保持这些位置前进。对于这个应用程序来说,这是一个有效和高效的方法。”
“从Cobalt的角度来看,它只是测量四个任意点云。然后,我们使用FARO Vantage激光跟踪仪在任何部件进入电池前记录这些位置,“ Asher说。“通过这种方式,你可以将它们组合在一起,以精确描绘零件。”
“毫无疑问,如果没有最初的激光跟踪器注册,这个应用将无法正常工作,”他说。“这是这个过程的一个重要的要求。”
自动化情况
Dynacraft工厂运行26条生产线。其中24个几乎全部是手动的,另外一个是半自动的 - 一个操作员和一个机器人。然后是新的QC线。
“这实际上是我们设施自动化程度最高的第一个项目,”Caudillo说。“我们的设施是劳动密集型的,所以当我们处理这个项目时,我们希望从一个手动的,劳动密集型的过程转变为高度自动化的过程。”
“这个系统是自给自足的,” Caudillo说。“ 根本没有运营商参与。系统将确定零件是好还是坏,是合格还是不合格,然后它会将该信息发送到生产线末端,以告诉我们的操作员是否装箱,无论是好的还是坏的部件。如果这是一个很好的部分,它将继续通过打包过程。如果这是一个不好的部分,VRSI系统会手动将该组件重新路由到返工站,在返工站进行返工,然后手动重新测量以验证它是否正确; 那么它会回到包装外面发货给我们的客户。”
最小化节拍时间
也许该项目的最大优先事项是满足节拍或周期时间要求。
Caudillo说:“65秒的生产线/生产周期必须生产出能够满足我们客户需求的零件。这65秒将允许我们每天建立大约240到250个组件。高于65秒的任何事物意味着生产线不符合客户的要求。”
产品进料和测量程序的高效自动化是开发能够满足生产周期时间的系统的重要因素。节省时间的另一个关键因素是Cobalt的机上处理,其中点云是在Cobalt内部计算的。
Asher说:“Cobalt的板载处理使应用程序如此无缝。一旦你掌握了Cobalt的位置和尺寸,这个点云就会在大约三到四秒内产生。快速这一点非常重要,因为这会让机器人有更多的时间移动。机器人不需要高速移动,因为Cobalt的速度让我们有了一定的灵活性。”
编辑推荐
最新资讯
-
辐射亚太,链接全球——采埃孚再制造
2025-07-30 11:46
-
思看科技发布子品牌SCANOLOGY,全球
2025-07-30 11:06
-
风雨不动安如山——比亚迪叉车构筑“
2025-07-30 08:48
-
NEAS CHINA 新能源汽车技术与生态链
2025-07-29 09:52
-
三维扫描革新碾磨机辊套检测,效率与
2025-07-25 10:46