简单分析内燃机气门感应热处理技术与质量控制
2018-01-04 17:10:36· 来源:金属加工 作者:王忠诚
内燃机气门是汽车发动机内提供动力的重要部件,尤其是排气门在高温、腐蚀性介质、长期重复的冲击,以及废气的冲刷作用下工作,因此既要具有良好的组织与强度,又要具有高的耐热性和热稳定性,良好的耐蚀性、抗咬合性、耐磨性和导热性等,其工作条件十分苛刻
内燃机气门是汽车发动机内提供动力的重要部件,尤其是排气门在高温、腐蚀性介质、长期重复的冲击,以及废气的冲刷作用下工作,因此既要具有良好的组织与强度,又要具有高的耐热性和热稳定性,良好的耐蚀性、抗咬合性、耐磨性和导热性等,其工作条件十分苛刻。因为气门的盘锥面与气门座圈反复接触,要求其有良好的耐磨性,而气门杆端面与凸轮接触,要求表面有高的硬度。因此,为满足其锥面与杆端的耐磨性,需要对气门进行锥面与杆端的淬回火处理,以获得要求的高硬度。通常是在马氏体耐热钢调质处理后再进行感应热处理。
本文仅对气门盘部锥面与杆部的感应淬火技术进行简单分析,并指出生产过程中出现的质量问题,且提出改进措施,旨在提高气门的感应淬火质量。
一、感应热处理在气门上的应用
1.感应热处理的特点
感应热处理是生产率高、不污染环境、易于自动化和节省能源的一种先进热处理技术。这一技术自问世以来一直在迅速发展,感应热处理技术的最大用户是汽车零部件领域。
感应热处理技术由于具有优质、高效、节能、环保等诸多优点,符合现代汽车生产需要,技术水平迅速提升[4]。高频感应加热设备在汽车零部件领域的应用十分广泛,如气门、挺杆、连杆、曲轴、凸轮轴、齿轮、万向节钟形壳及半轴等,其中气门杆端进行连续淬火或冲击淬火,锥面进行自动连续作业成为国内外气门感应热处理最成功的技术,获得了气门制造厂商的青睐,国内100余家气门制造厂商均拥有5台以上的高频设备。其中我公司有30余台感应淬火设备(或连续生产线),年产感应淬火气门2000万支以上,成为中国气门制造厂商中产量最大与出口数量最多的制造厂商之一。
2. 内燃机气门感应淬火的基本要求
气门热处理(调质处理)后进行感应淬火,目的是满足其杆端面(或锥面)耐磨的要求, 《内燃机 进、排气门 技术条件》(GB/T23337—2009)与《汽车发动机气门技术条件》(QC/T469—2002)中,均指出杆端面经过表面淬火后硬度应≥48HRC,当杆端部长度>4mm时,硬化层深度应≥2mm)或淬硬层深度应≥0.6mm。盘锥面经过表面淬火后的硬化层应≥1.5mm,其硬度值应符合图样规定,杆端与锥面感应淬火晶粒度细于8级。可见对气门的锥面与杆部进行感应淬火是标准所要求的,是提高气门表面硬度的不可缺少的热处理手段。
二、气门感应热处理的技术要求、感应器的形式与选用
1. 技术要求
气门进行感应淬火的技术要求包括表面(或端面)硬度、硬化层(淬火)深度或长度、金相组织、畸变量及外观等。
(1)锥面淬火要求 气门锥面(阀口)与气门底座反复贴合,要求其表面具有高的硬度和良好的耐磨性,感应淬火可满足其要求。锥面淬火的锥面硬度在45~58HRC,硬化层深度一般≥1.5mm,晶粒度细于8级,某气门锥面淬火技术要求如图1所示(图中A点位置:距盘端面1.7mm,距盘外圆3.3mm。要求在淬火深度测量时应透过A点,淬火区及过渡区不得超过图中粗实线)。
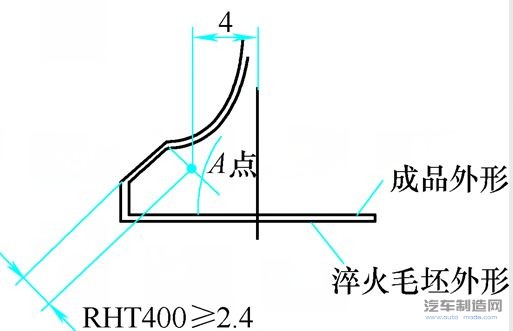
图1 某气门锥面工艺要求的淬火深度与硬度
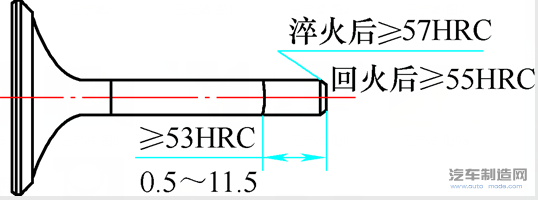
图2气门杆部淬透要求
(2)杆端淬火要求 对于气门杆部的技术要求为淬火硬度50~60HRC,硬化层深度≥2mm,晶粒度细于8级等,其中工艺要求有杆部淬透、仿形淬火、杆端冲击淬火等,图2、图3、图4为某些气门杆部淬透、杆部仿形和杆端冲击淬火的技术要求。
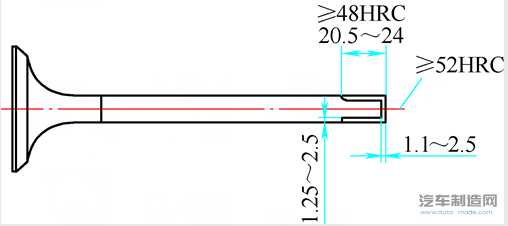
图3气门杆部仿形淬火要求
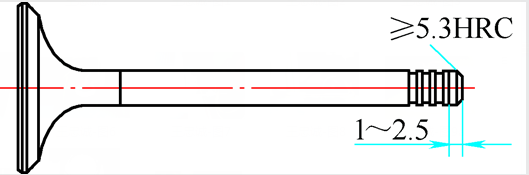
图4 气门杆端冲击淬火要求
2. 感应器的形式与选用
(1)锥面淬火感应器 锥面淬火采用专用的感应器,通常气门使用的锥面淬火感应器有两种:连续式感应器与单圈感应器,其形状是根据气门盘锥面确定的,图5、图6为常见的感应器形式。

图5 多工位气门锥面淬火感应器实物形态
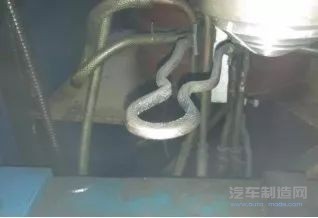
图6单圈气门锥面淬火感应器
锥面淬火感应器的选用原则:感应器内沿与气门锥面之间留有间隙为1.5~3mm,气门的盘部在加热过程中是旋转的,具体参数如电流、电压、频率、加热温度与加热时间是通过工艺试验来进行确定的,即满足硬度与淬火深度合格,晶粒度要细于8级的要求,锥面淬火后的气门通常进行160~200℃低温回火或高温回火处理,以稳定组织,减小内应力与脆性。
(2)杆端淬火感应器 气门的杆端淬火采用特制的感应器。这是考虑到其技术要求的差异而设计的,同时其工艺参数也有较大的不同,目的是满足杆部的不同硬度与淬火长度的要求。图7、图8为冲击与仿形淬火感应器,图9为杆端连续淬火与连续淬回火感应器,该类感应器应用十分普遍,生产效率高。
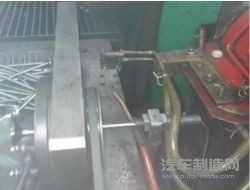
图7气门杆端冲击/仿形淬火感应器
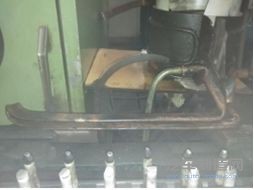
图8 气门杆部淬透连续淬火感应器
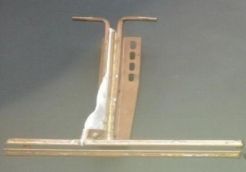
(a)回火感应器
(b)淬火感应器
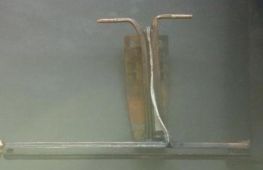
图9 气门杆部连续式淬火与回火感应器
三、气门感应热处理的质量控制
1. 过程质量控制
为满足气门感应淬火后的质量符合技术要求,气门应进行锥面和杆端感应淬火的加热与冷却,选用感应器、喷水器的结构、形状及尺寸应满足使用要求。根据工艺试验结果确定最佳的工艺参数等,并按如下要求进行:
(1)要确定电压、电流、加热温度、加热时间或进给速度等。
(2)介质温度、压力、流量、浓度的范围及冷却时间。
(3)感应器外观与冷却喷淋结构符合要求。
2. 质量检查方法
目前气门杆部与锥面的硬度、长度或深度、晶粒度等检查方法采用以下要求进行:
(1)对于要求采用洛氏/维式硬度检查和淬火长度则采用在锥面或杆部外圆上检查,图10为检查图片。
(2)对于要求采用维氏硬度(平面)检查的,则是在剖开锥面或杆部平面上,抛光后硬度与长度等按要求检查如图11所示。
(3)晶粒度的检查按要求抛光腐蚀后进行。
(a)锥面硬度检查 (b)杆端硬度检查 (c)杆部淬火长度检查
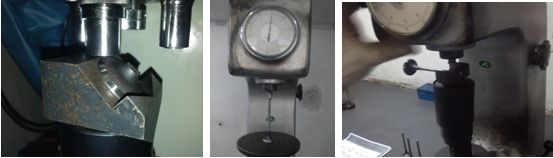
图10 气门硬度与淬火长度的硬度检查法
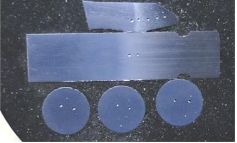
图11 气门锥面与杆端与淬火长度检查(硬度法)
3. 缺陷形式与原因分析
气门锥面与杆端淬火缺陷形式与原因分析具体见附表。
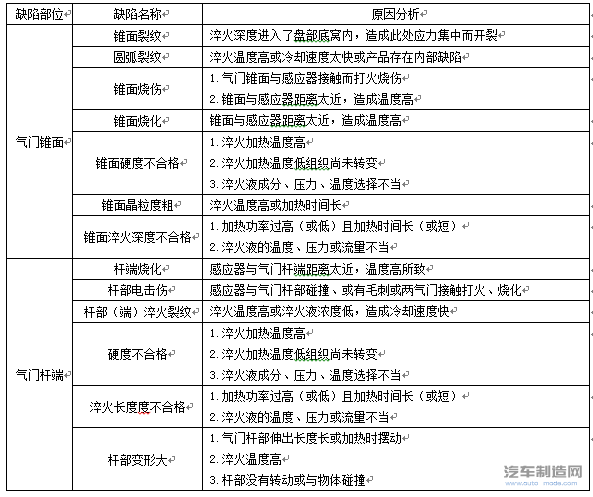
气门感应热处理缺陷形式与原因分析
四、气门感应热处理的最新动态与发展动向
1.最新动态
(1)进行头杆与杆杆焊气门的摩擦焊接后的快速退火处理,可进行连线加工,气门在连续式感应器中加热,取消了焊后气门集中退火繁琐工序,实现节能降耗。国外气门制造厂商开始在部分气门生产线上应用该技术。
(2)用于头杆焊气门脖颈处校直前的加热,尤其对于不允许进行冷矫直或锤击盘部(手工锤击,容易造成盘部掉块或存在隐患)的气门采用此类措施,可根除柴油机气门早期失效的发生。
(3)目前奥氏体耐热钢条材是制造气门的原材料,是热轧材经高温固溶处理制成,为保证气门的使用性能,固溶处理大多采用电炉、燃气炉、盐浴炉等。感应加热固溶处理可以达到传统固溶处理的目的,采用超音频电源实现在居里点以下温度具有良好的电效率,固溶处理温度在1100~1150℃,时的吨钢电能消耗为350~400kW·h,加热系统的电效率可以达到65%左右。
2.发展动向
(1)向自动化方向发展,减轻劳动强度,提升生产效率。
气门采用自动上下料自动进行锥面和杆端的淬火处理,出现异常或故障,设备自动报警,从根本上解决依靠操作者进行繁琐的重复劳动的弊端,产品质量稳定与生产效率明显提高。
(2)向智能化方向发展,进行预防控制,实现报警、高低温产品的分离等功能。
1)按工艺要求输入程序后采用计算机控制,操作屏幕界面清晰,各种动作指令触屏即可完成,人员进行巡视即可,从而减少人为因素的影响,确保产品质量的稳定与一致性。
2)对电源的运行状态及参数实时监控(如电压、电流、功率、频率、温度等),真正实现实时了在线监控。
3)计算机模拟感应热处理已在部分企业、研究所开展。这样虚拟试制新技术将替代繁琐费时的现场工艺调整。
本文仅对气门盘部锥面与杆部的感应淬火技术进行简单分析,并指出生产过程中出现的质量问题,且提出改进措施,旨在提高气门的感应淬火质量。
一、感应热处理在气门上的应用
1.感应热处理的特点
感应热处理是生产率高、不污染环境、易于自动化和节省能源的一种先进热处理技术。这一技术自问世以来一直在迅速发展,感应热处理技术的最大用户是汽车零部件领域。
感应热处理技术由于具有优质、高效、节能、环保等诸多优点,符合现代汽车生产需要,技术水平迅速提升[4]。高频感应加热设备在汽车零部件领域的应用十分广泛,如气门、挺杆、连杆、曲轴、凸轮轴、齿轮、万向节钟形壳及半轴等,其中气门杆端进行连续淬火或冲击淬火,锥面进行自动连续作业成为国内外气门感应热处理最成功的技术,获得了气门制造厂商的青睐,国内100余家气门制造厂商均拥有5台以上的高频设备。其中我公司有30余台感应淬火设备(或连续生产线),年产感应淬火气门2000万支以上,成为中国气门制造厂商中产量最大与出口数量最多的制造厂商之一。
2. 内燃机气门感应淬火的基本要求
气门热处理(调质处理)后进行感应淬火,目的是满足其杆端面(或锥面)耐磨的要求, 《内燃机 进、排气门 技术条件》(GB/T23337—2009)与《汽车发动机气门技术条件》(QC/T469—2002)中,均指出杆端面经过表面淬火后硬度应≥48HRC,当杆端部长度>4mm时,硬化层深度应≥2mm)或淬硬层深度应≥0.6mm。盘锥面经过表面淬火后的硬化层应≥1.5mm,其硬度值应符合图样规定,杆端与锥面感应淬火晶粒度细于8级。可见对气门的锥面与杆部进行感应淬火是标准所要求的,是提高气门表面硬度的不可缺少的热处理手段。
二、气门感应热处理的技术要求、感应器的形式与选用
1. 技术要求
气门进行感应淬火的技术要求包括表面(或端面)硬度、硬化层(淬火)深度或长度、金相组织、畸变量及外观等。
(1)锥面淬火要求 气门锥面(阀口)与气门底座反复贴合,要求其表面具有高的硬度和良好的耐磨性,感应淬火可满足其要求。锥面淬火的锥面硬度在45~58HRC,硬化层深度一般≥1.5mm,晶粒度细于8级,某气门锥面淬火技术要求如图1所示(图中A点位置:距盘端面1.7mm,距盘外圆3.3mm。要求在淬火深度测量时应透过A点,淬火区及过渡区不得超过图中粗实线)。
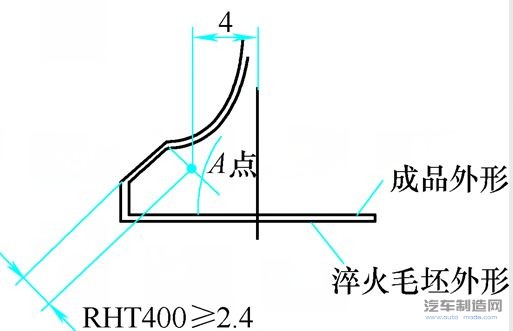
图1 某气门锥面工艺要求的淬火深度与硬度
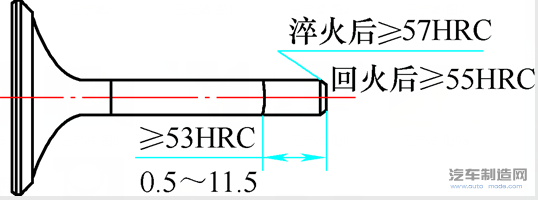
图2气门杆部淬透要求
(2)杆端淬火要求 对于气门杆部的技术要求为淬火硬度50~60HRC,硬化层深度≥2mm,晶粒度细于8级等,其中工艺要求有杆部淬透、仿形淬火、杆端冲击淬火等,图2、图3、图4为某些气门杆部淬透、杆部仿形和杆端冲击淬火的技术要求。
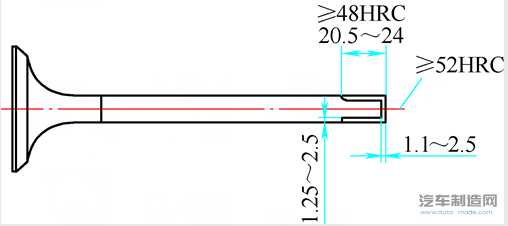
图3气门杆部仿形淬火要求
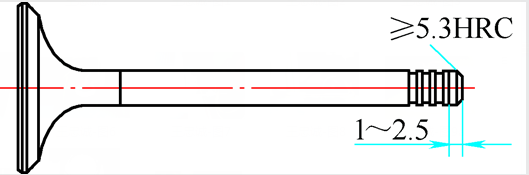
图4 气门杆端冲击淬火要求
2. 感应器的形式与选用
(1)锥面淬火感应器 锥面淬火采用专用的感应器,通常气门使用的锥面淬火感应器有两种:连续式感应器与单圈感应器,其形状是根据气门盘锥面确定的,图5、图6为常见的感应器形式。

图5 多工位气门锥面淬火感应器实物形态
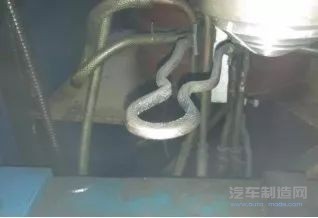
图6单圈气门锥面淬火感应器
锥面淬火感应器的选用原则:感应器内沿与气门锥面之间留有间隙为1.5~3mm,气门的盘部在加热过程中是旋转的,具体参数如电流、电压、频率、加热温度与加热时间是通过工艺试验来进行确定的,即满足硬度与淬火深度合格,晶粒度要细于8级的要求,锥面淬火后的气门通常进行160~200℃低温回火或高温回火处理,以稳定组织,减小内应力与脆性。
(2)杆端淬火感应器 气门的杆端淬火采用特制的感应器。这是考虑到其技术要求的差异而设计的,同时其工艺参数也有较大的不同,目的是满足杆部的不同硬度与淬火长度的要求。图7、图8为冲击与仿形淬火感应器,图9为杆端连续淬火与连续淬回火感应器,该类感应器应用十分普遍,生产效率高。
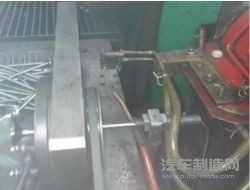
图7气门杆端冲击/仿形淬火感应器
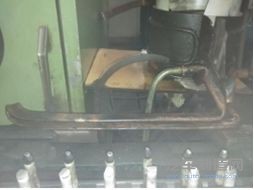
图8 气门杆部淬透连续淬火感应器
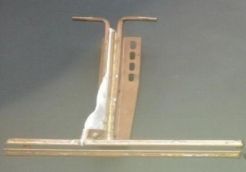
(a)回火感应器
(b)淬火感应器
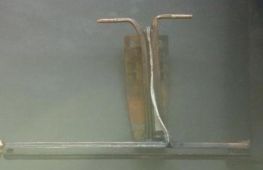
图9 气门杆部连续式淬火与回火感应器
三、气门感应热处理的质量控制
1. 过程质量控制
为满足气门感应淬火后的质量符合技术要求,气门应进行锥面和杆端感应淬火的加热与冷却,选用感应器、喷水器的结构、形状及尺寸应满足使用要求。根据工艺试验结果确定最佳的工艺参数等,并按如下要求进行:
(1)要确定电压、电流、加热温度、加热时间或进给速度等。
(2)介质温度、压力、流量、浓度的范围及冷却时间。
(3)感应器外观与冷却喷淋结构符合要求。
2. 质量检查方法
目前气门杆部与锥面的硬度、长度或深度、晶粒度等检查方法采用以下要求进行:
(1)对于要求采用洛氏/维式硬度检查和淬火长度则采用在锥面或杆部外圆上检查,图10为检查图片。
(2)对于要求采用维氏硬度(平面)检查的,则是在剖开锥面或杆部平面上,抛光后硬度与长度等按要求检查如图11所示。
(3)晶粒度的检查按要求抛光腐蚀后进行。
(a)锥面硬度检查 (b)杆端硬度检查 (c)杆部淬火长度检查
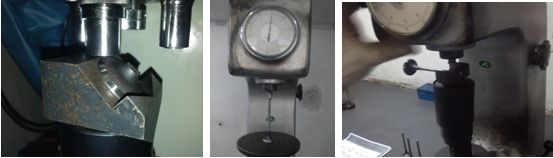
图10 气门硬度与淬火长度的硬度检查法
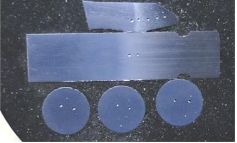
图11 气门锥面与杆端与淬火长度检查(硬度法)
3. 缺陷形式与原因分析
气门锥面与杆端淬火缺陷形式与原因分析具体见附表。
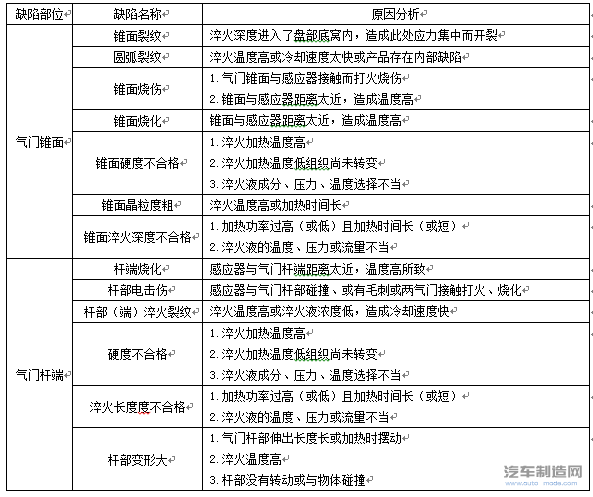
气门感应热处理缺陷形式与原因分析
四、气门感应热处理的最新动态与发展动向
1.最新动态
(1)进行头杆与杆杆焊气门的摩擦焊接后的快速退火处理,可进行连线加工,气门在连续式感应器中加热,取消了焊后气门集中退火繁琐工序,实现节能降耗。国外气门制造厂商开始在部分气门生产线上应用该技术。
(2)用于头杆焊气门脖颈处校直前的加热,尤其对于不允许进行冷矫直或锤击盘部(手工锤击,容易造成盘部掉块或存在隐患)的气门采用此类措施,可根除柴油机气门早期失效的发生。
(3)目前奥氏体耐热钢条材是制造气门的原材料,是热轧材经高温固溶处理制成,为保证气门的使用性能,固溶处理大多采用电炉、燃气炉、盐浴炉等。感应加热固溶处理可以达到传统固溶处理的目的,采用超音频电源实现在居里点以下温度具有良好的电效率,固溶处理温度在1100~1150℃,时的吨钢电能消耗为350~400kW·h,加热系统的电效率可以达到65%左右。
2.发展动向
(1)向自动化方向发展,减轻劳动强度,提升生产效率。
气门采用自动上下料自动进行锥面和杆端的淬火处理,出现异常或故障,设备自动报警,从根本上解决依靠操作者进行繁琐的重复劳动的弊端,产品质量稳定与生产效率明显提高。
(2)向智能化方向发展,进行预防控制,实现报警、高低温产品的分离等功能。
1)按工艺要求输入程序后采用计算机控制,操作屏幕界面清晰,各种动作指令触屏即可完成,人员进行巡视即可,从而减少人为因素的影响,确保产品质量的稳定与一致性。
2)对电源的运行状态及参数实时监控(如电压、电流、功率、频率、温度等),真正实现实时了在线监控。
3)计算机模拟感应热处理已在部分企业、研究所开展。这样虚拟试制新技术将替代繁琐费时的现场工艺调整。
最新资讯
-
辐射亚太,链接全球——采埃孚再制造
2025-07-30 11:46
-
思看科技发布子品牌SCANOLOGY,全球
2025-07-30 11:06
-
风雨不动安如山——比亚迪叉车构筑“
2025-07-30 08:48
-
NEAS CHINA 新能源汽车技术与生态链
2025-07-29 09:52
-
三维扫描革新碾磨机辊套检测,效率与
2025-07-25 10:46