用于汽车制造的瓦尔特新槽型-曲轴油孔钻
2017-10-27 14:01:01·
图宾根瓦尔特的业务开发和零件运输经理Harald Preue先生问题:Preue 老师, 我们都知道,总部位于图宾根的瓦尔特为全世界的汽车制造商和供应商提供更加高效的制造工艺过程所用的刀具和解决方案。今天您讲的曲轴油孔钻有有哪些优势和特点
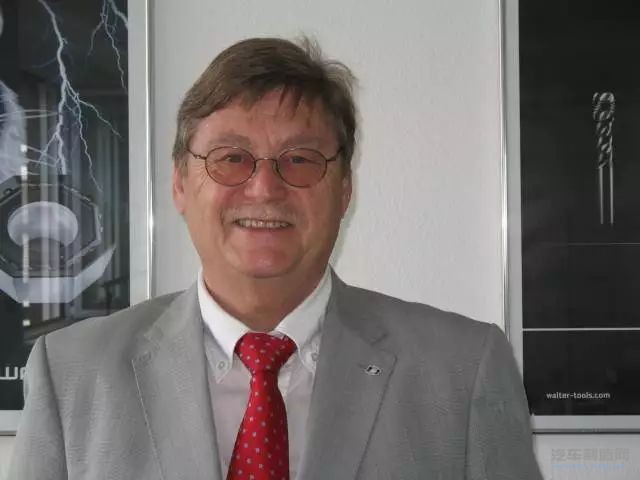
图宾根瓦尔特的业务开发和零件运输经理Harald Preuße先生
问题:Preuße 老师, 我们都知道,总部位于图宾根的瓦尔特为全世界的汽车制造商和供应商提供更加高效的制造工艺过程所用的刀具和解决方案。今天您讲的曲轴油孔钻有有哪些优势和特点?我们要掌握哪些技术特性?
Preuße 老师: 采用新排屑槽型的钻头进行油孔钻孔,排屑效果好,刀具寿命长,加工稳定性高,并且支持环保和成本节省的微量油雾润滑(MQL)。
曲轴油孔钻头本身面临挑战。其中最关键的调整之一是钻孔深度及其引起的后果。钻孔深度通常为20倍径或以上。可与DC 173配套使用:直径为6毫米的钻孔通常用于乘用车曲轴,钻孔深度可达120毫米,甚至150毫米。在极端情况下,油孔深度可达30倍径。
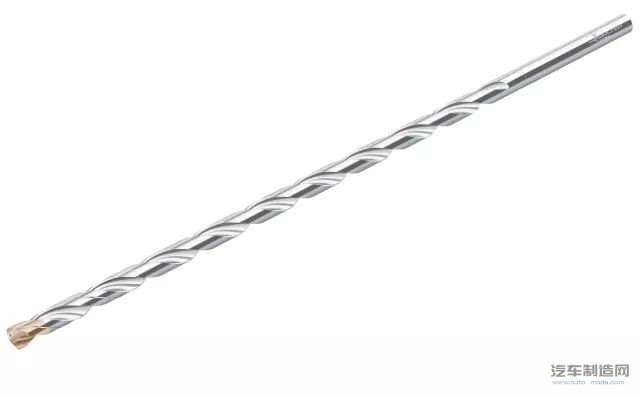
根据制造和车型的不同,工件可采用铸造合金或钢制成。通常抗拉强度为800~1200牛米(Nm)。乘用车大约80%的油孔直径为4~8毫米,商用车曲轴油孔直径5~6毫米为惯例,7~8毫米为标准。
挑战:深钻孔排屑
问题::特别是钢制曲轴,例如那些商用车曲轴,钻孔深度最容易出现问题:排屑要平稳干净。如果钻头穿孔工件,通常会形成很长的螺旋形切屑。如果钻孔深度为孔径的5倍,则排屑较为困难。如何解决这些问题呢?
Preuße 老师: 我们研发新钻头的排屑槽型时,改变了钻尖部份的核心槽型,采用这种方式后,不会形成长屑,现在钻孔形成的是逗号形状的碎屑。因为短碎屑不会被堵在钻孔与刀具之间,所以排屑更容易。采用新的槽型后,处理刀具尖部小平面尺寸太大时形成的残留钻屑不再是问题。
瓦尔特工程师研发的新槽型还做了一些其它改进。采用当今大多数加工理念和刀具,在钻深孔时的工艺过程必须中断才能排屑。采用我们的新刀具后,我们可钻极其深的孔,并且能一直钻到底,因为中途没有钻屑堵塞,这比以前的效率高多了。
油孔钻孔的位置和过程
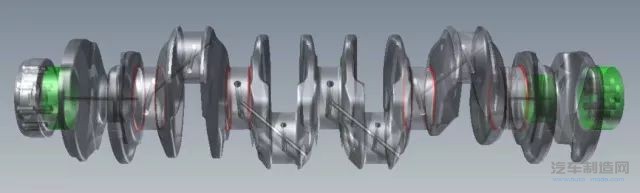
当使用铸铁时,独特的小平面使磨损量最小
铸铁工件的加工条件不同。一般来说,铸铁加工比钢材容易。但是,特别是灰口铸铁会使刀具在角落处磨损得更快。为了防止这种情况,瓦尔特研发人员设计出了新油孔钻头,用于铸铁钻孔,形成独特的小平面。
瓦尔特研发团队很自豪的是研发出的产品使微量油雾润滑(MQL)更高效。微量油雾润滑系指加工过程中每小时消耗的冷却润滑液不到20毫升。
不采用传统乳化液或冷却油的湿式加工,新产品采用油-空气冷却并且对刀具及加工工件表面润滑。工艺过程余热通过刀具和钻屑排除。除了冷却液分配和供应可靠外,安全排屑对微量油雾润滑也很重要。瓦尔特的新槽型有明显的排屑优势。
挑战:深钻孔排屑
问题::广泛采用微量油雾润滑的原因有哪些?它又能带来哪些功效?
Preuße 老师:原因有多种。一方面,采用微量油雾冷却液润滑,具有明显的财务效益:
微量油雾润滑每小时仅需10~20冷却润滑液,而不是500升以上。因此,采用微量油雾润滑,几乎全部不需要冷却液的采购费用、贮存费用和运输费用。
冷却液和湿屑必须按特殊废物处置。这比新鲜油还昂贵。相反,干屑还可当做再生材料销售。
采用微量油雾润滑,几乎全部不采用冷却液的处置技术和后续昂贵的工件清洁过程。
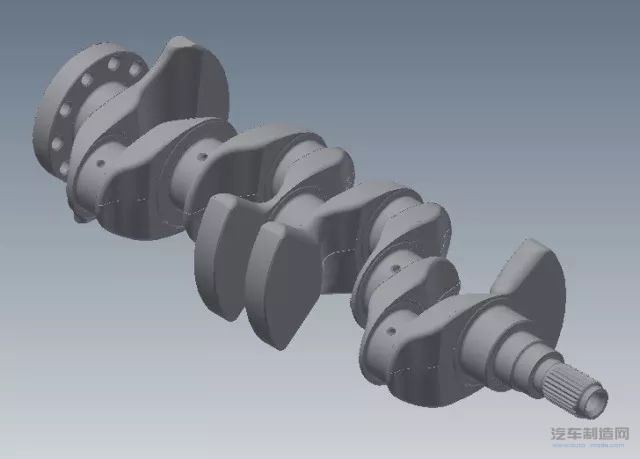
曲轴
另外,可减小润滑剂的用量,清洁环保。这些优势已被生产商向其客户证明了多年。油雾不会导致工作场所事故和机床操作人员的健康危害。
但是,采用微量油雾工作,以前对大多数加工概念都不适用,如果传统加工概念使用微量油雾润滑,平均性能损失20%~30%。但是,使用瓦尔特新刀具,情况大不一样。瓦尔特的新槽型保证在使用微量油雾润滑后,刀具和工件的性能与使用大量油或乳化液的其它加工概念完全一样。
经过全球现场试验
上市前,我们瓦尔特团队对其研发的新产品进行了现场试验,并按计原计划上市。我们拜访了世界上一些最大的制造厂,他们在各种不同条件下对我们的刀具进行了试验。
试验时,完全不改变客户现有的机床条件和外围加工设备,并将用新刀具获得的数据与用以前的刀具获得的数据相比。
结果不言而喻:“我们现在刀具使用寿命几乎比以前的解决方案长50%~100%。” 每把刀具80~110米的刀具寿命很常见。瓦尔特新刀具在一致的条件下可到达160~200米,最高可达300米。另外,加工稳定性特别高。“新刀具的效率也与其它深钻孔差不多。”
瓦尔特新油孔钻头已经上市几个月。这些钻头当作非标刀具销售,但是交货时间很短。如果订单量小于50套,瓦尔特可在四周内交货,大批量订单的交货时间最长8周。
我总结一下:“据我知道,市面上目前还没有其它曲轴钻孔方法可达到这种高水平的加工稳定性和效率,而且还适合大量的加工工艺过程。实际上,进行试验的所有用户都抢着用我们的新刀具。”
最新资讯
-
江淮成立新公司
2024-05-08 08:21
-
广汽海外首个保税工厂正式获批,泰国
2024-05-08 08:08
-
底盘紧固件开发的流程和关键技术
2024-05-08 08:02
-
某高强钢汽车控制臂冲压成形工艺研究
2024-05-08 07:54
-
电车用电池包生产过程
2024-05-07 10:20